Nautique
Elevating marine design with sustainable solutions.
Shaped Foam Kits
Advanced Shaped Foam Kits for lightweight construction
Thermoformed foam core has been used for decades by leading boatbuilders to reduce weight and improve hull properties versus foam with cross cuts, which fill with resin. bespline further improves this construction, increasing impact resistance and durability by reducing previous rigid lines of resin which reduces wasted material and cost.
bespline Facts
Up to 25% less resin.
Up to 5X faster to install.
Up to 4X energy absorption.
Engineering
Precision engineering for optimized Shaped Foam Kits
From our customer’s 3D drawings/CAD files, we split the hulls into panels optimized to minimize core waste. We generate the Shaped Foam Kit core map with features such as chamfers, cut-outs and inserts marked in each panel drawing. Panel shape and thickness are analyzed, and spring-back correction is applied. Our software then converts the finalized Shaped Foam Kit drawings into the control program for our adaptive mold.
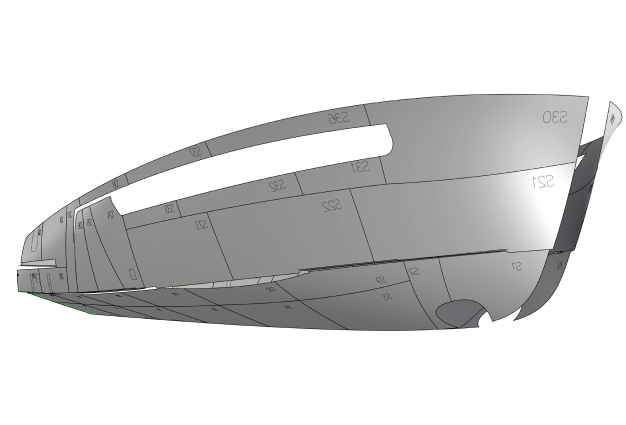
Production and Installation
Each Shaped Foam Kit panel is thermoformed on our adaptive mold.
- Trimming lines and cut-outs are marked using a laser projector.
- Panels are trimmed and chamfered to net shape.
- Inserts and other features are CNC machined.
- Panels are then labeled per the Shaped Foam Kit core map, packed and shipped to the customer.
We ship the Shaped Foam Kit with the 3D core map and work instructions for the panel fitting procedure. We can also provide on-site installation support.
- Trimming lines and cut-outs are marked using a laser projector.
- Panels are trimmed and chamfered to net shape.
- Inserts and other features are CNC machined.
- Panels are then labeled per the Shaped Foam Kit core map, packed and shipped to the customer.
We ship the Shaped Foam Kit with the 3D core map and work instructions for the panel fitting procedure. We can also provide on-site installation support.
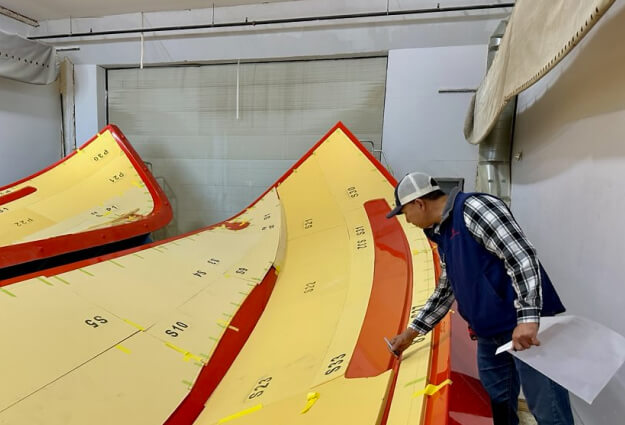
Capabilities, Benefits
Advanced thermoforming capabilities and benefits
- Thermoforming up to 180°C
- Assembly of large panels up to 2040 x 3240 mm
- Single or double curvature radius up to 350 mm
- Surface accuracy of +/-1mm
- SAN copolymer and recycled PET foam cores
The mapping and nesting service we provide ensures minimal material waste, while the correction for springback guarantees a better fitting core kit for reduced assembly times. Cores up to 50 mm thick can be thermoformed with a unique process, saving kilograms of resin and hours of labor.
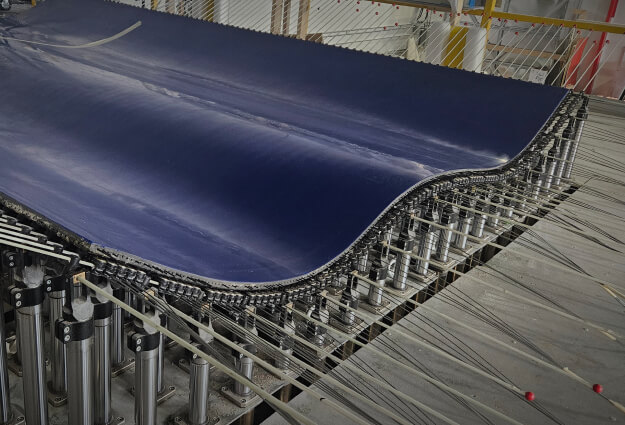
Case Studies
Discover our innovative solutions for complex challenges
Finishes
bespline also offers labor, weight and cost savings
Thin plies are cross-laminated with decorative veneers and/or cores in a cold-forming process on our adaptive mold. These incredibly lightweight, strong and beautiful panels enable free-form designs — with strength, stiffness, shape and thickness tailored for each application.
Materials and Finishes
We work with a wide range of materials and finishes, meeting not only unique aesthetics but also noise and thermal insulation, fire resistance and other requirements.
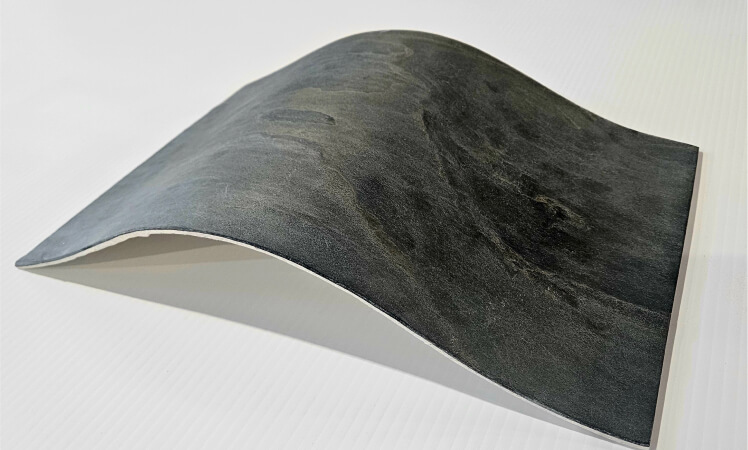