Technology
Adaptive Mold System
bespline uses a digitally controlled reconfigurable tool/adaptive mold system to create singly- and doubly-curved shapes from 3D CAD files.
This system comprises a membrane on top of actuators that create the precision shape in minutes.
From our customer’s 3D drawings/CAD files, we split the final structure into panels optimized to minimize waste. We generate drawings with features marked such as chamfers, cut-outs and inserts. Panel shape and thickness are analyzed, and spring-back correction is applied. Our software then converts the finalized panel drawings into the control program for our adaptive mold.
Adaptive Mold System
The adaptive mold enables fast, efficient and sustainable 3D shaping of various materials:
Foam cores (e.g., SAN copolymer, recycled PET)
Wood veneers, solid and laminated wood
Fiber-reinforced laminates.
Trimming lines and cut-outs are marked using a laser projector.
We provide our Shaped Foam Kits with each piece labeled and illustrated in a 3D core map with work instructions for panel fitting/installation.
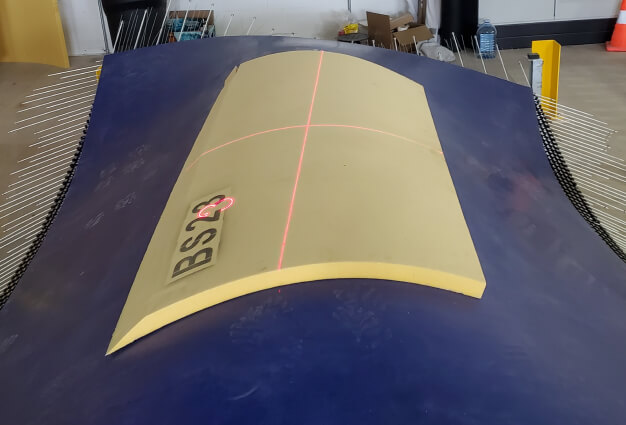
Process Specifications and Assemblies
bespline’s process features a range of capabilities:
Thermoforming up to 180°C
Single curvature or double curvature, radius up to 350mm
Surface accuracy of +/-1mm
Cores up to 50 mm thick and 450 kg/m3 can be thermoformed with a unique process, saving kilograms of resin and hours of labor
Shaped panels up to 2040mm x 3240mm can be produced and assembled to create large structures
For such multi-component structures — e.g., cockpits and simulator domes — we produce the shaped pieces and assemble them as approved by our engineer-customer team. We install fasteners and other features and then proceed with finishing.
bespline shaped parts and assemblies come with a primer, ready to paint, or painted to match any RAL color. We also offer a range of materials and finishes using novel technologies to achieve unique aesthetics as well as fire resistance, noise insulation and more.
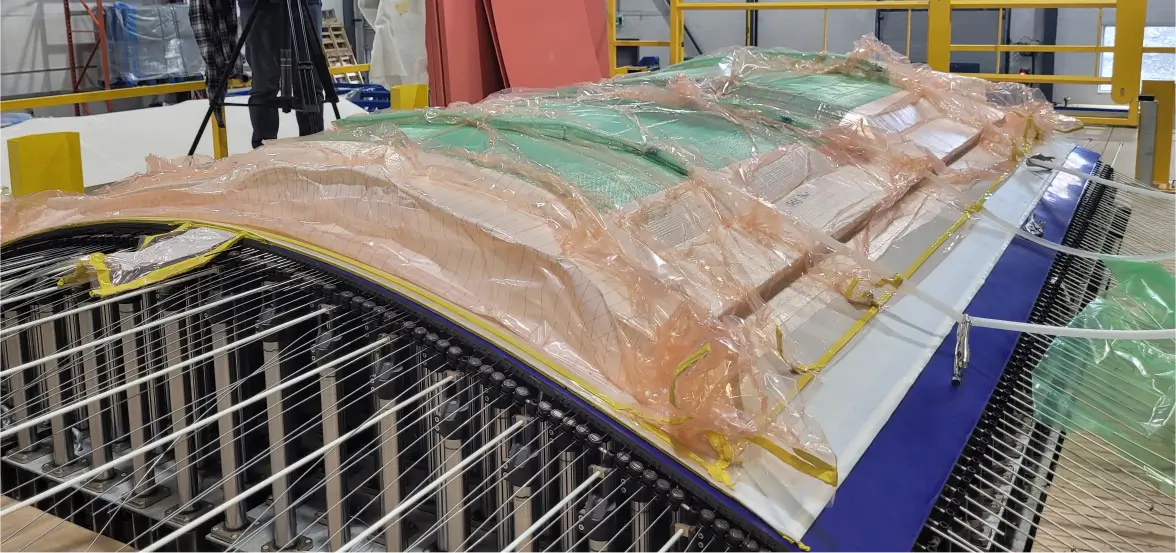
Composite Materials
bespline uses wet layup, prepreg or vacuum-assisted infusion processes to create 3D shaped laminates on its adaptive mold.
Resins — epoxy, polyester, thermoplastic and FR VOC-free acrylic but others are possible.
Reinforcements — glass, carbon, basalt and/or natural fibers such as flax.
Formats — woven, NCF, unidirectional, nonwovens, films and foils. bespline's adaptive mold technology also enables us to develop new processing techniques and material approaches that were previously not possible.
New Solutions
bespline continues to develop new materials and process options for future solutions.
We work with our sister company, Addcomp, and our industry partners to push the boundaries of what is possible in aesthetics and finishes, more sustainable materials, new multifunctionalities and capabilities for our customers. What future products can you envision?
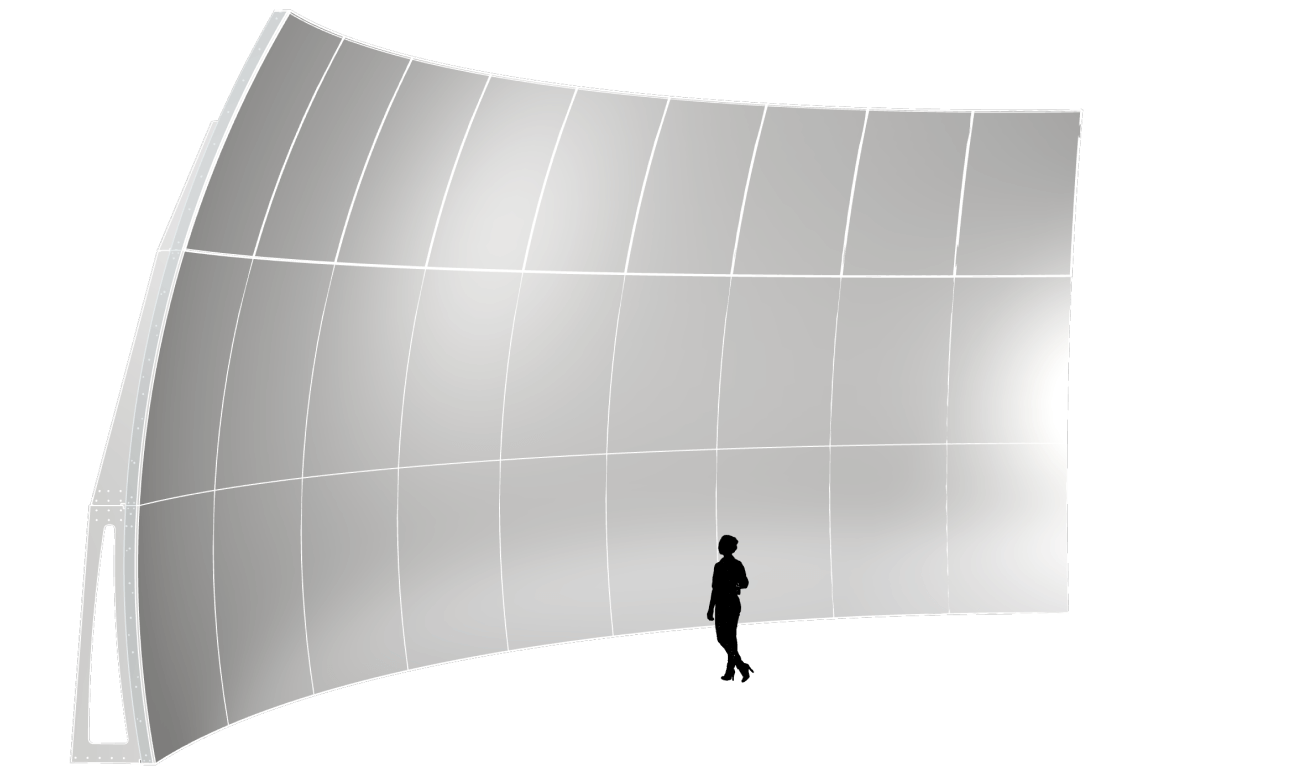